
STAR HOUR BauMinator®
O jedną trzecią mniej betonu i stali. 25% mniej CO2. Dla największego na świecie sufitu tego typu.
BauMinator® działał przez całą dobę,do 52 godzin jednocześnie.
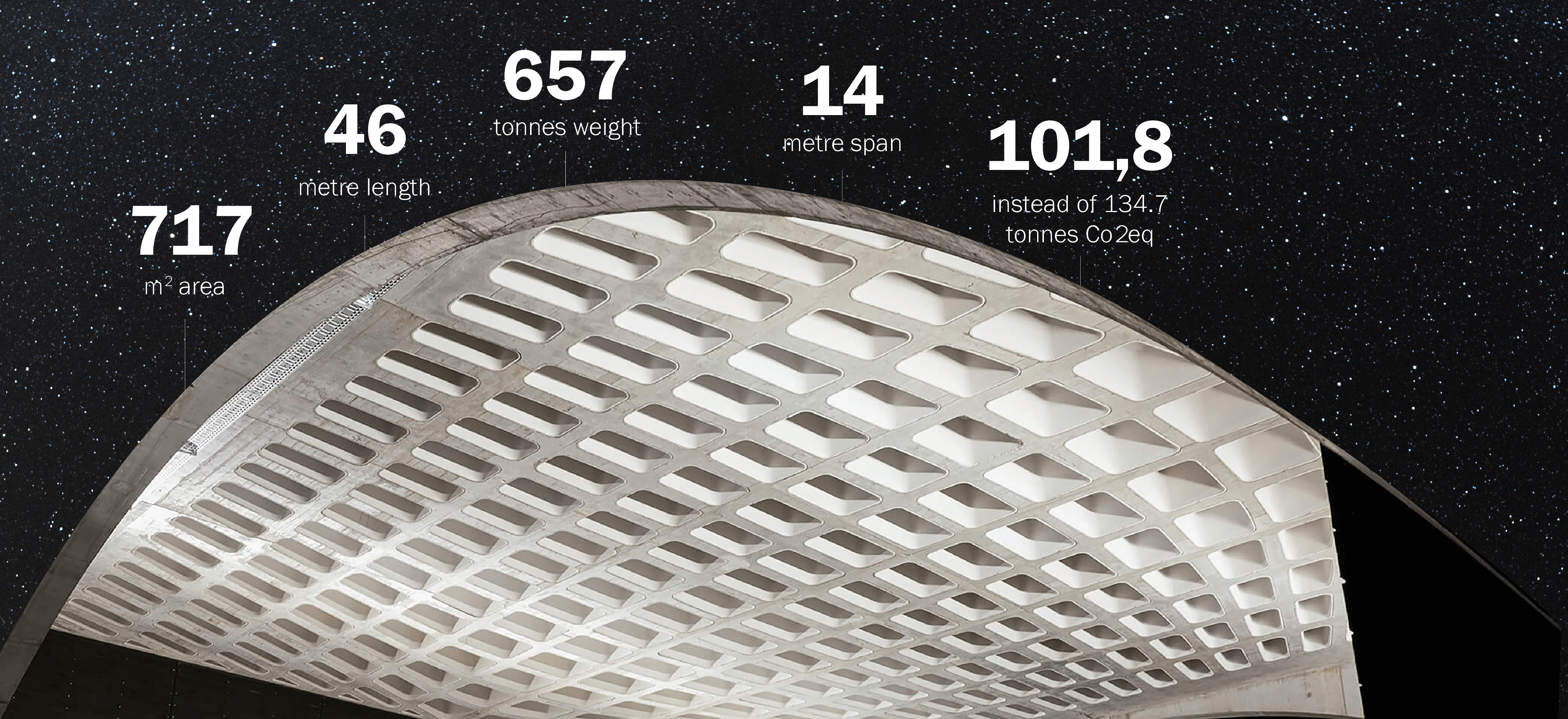
Koncentracja na oszczędzaniu materiałów
Wszyscy zaangażowani w projekt dążyli do wykorzystania jak najmniejszej ilości materiałów. Baumit Austria dostarczył system i materiały na potrzeby projektu. „Dzięki drukowi 3D możemy używać betonu bez żadnych szalunków. Technologia ta pozwala nam tworzyć nowe geometrie bez odpadów. Oszczędza to beton i stal” – wyjaśnia Georg Hansemann z Politechniki w Grazu.
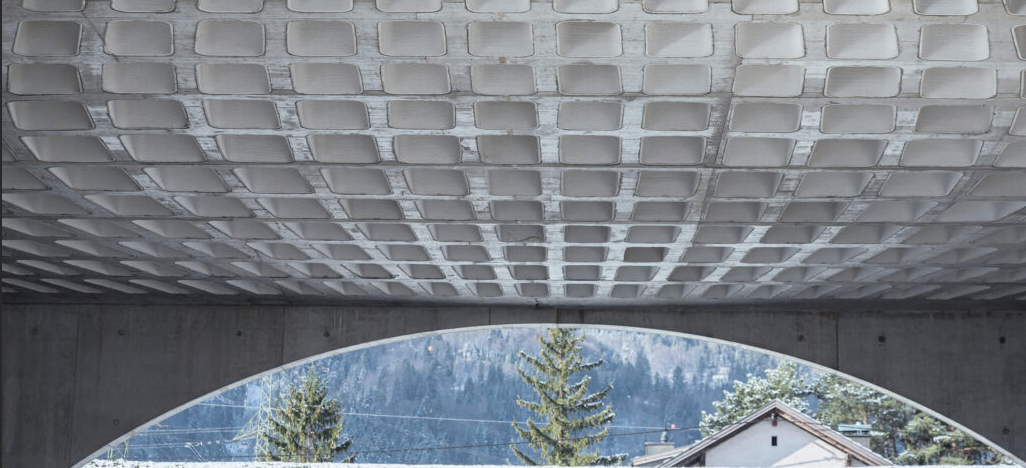
792 korpusy wypornościowe dla dachu płaskiego - każda z nich jest wyjątkowa, każdy ponumerowany.
Lekkie i przyjazne dla klimatu rozwiązanie
Instalacja szalunku traconego z drukarki 3D oszczędza materiał i emisje. Korzystając ze specjalnie zakupionego oprogramowania, obliczono 792 przemieszczenia dla płaskiego dachu o powierzchni 717 metrów kwadratowych – każde z nich było unikalne. Zostały one wydrukowane przy użyciu ponad 60 ton betonu i łącznie 210 kilometrów linii drukarskiej. Ważące do 80 kilogramów elementy zostały ponumerowane, dostarczone na plac budowy i ustawione na szalunku za pomocą tachimetru. Pomiędzy nimi ułożono stal zbrojeniową, a całość wypełniono betonem. Zadowalającym rezultatem był sufit, który był o jedną trzecią lżejszy, a jego produkcja emitowała o 24,4% mniej gazów cieplarnianych.
33 tony szkodliwych dla klimatu gazów cieplarnianych zaoszczędzonych podczas produkcja.
Największy na świecie sufit z tym systemem
Architekt Marcus Ender zwraca uwagę na możliwości projektowe tej technologii. „Kształt i rozmieszczenie wgłębień uwidaczniają przebieg sił”. Specjalna obsługa i pomysłowa logistyka naturalnie spowodowały dodatkowe koszty. Zostało to jednak zrekompensowane oszczędnościami materiałowymi i rozszerzonymi możliwościami konstrukcyjnymi.
Płaski dach spoczywa na dwóch 46-metrowe łuki podtrzymujące, które obejmują dwie drewniane hale.
Przykład gospodarki o obieguzamkniętym
Projekt nadaje się również do recyklingu ze względu na skład materiału. Konstrukcja składa się w całości z betonu i stali, dzięki czemu może być w 100% poddana recyklingowi po zakończeniu okresu użytkowania. Uniwersytet Techniczny w Grazu ma dalszy potencjał w zakresie stosowania betonu o obniżonej emisji CO2, jak również w zakresie procesu.
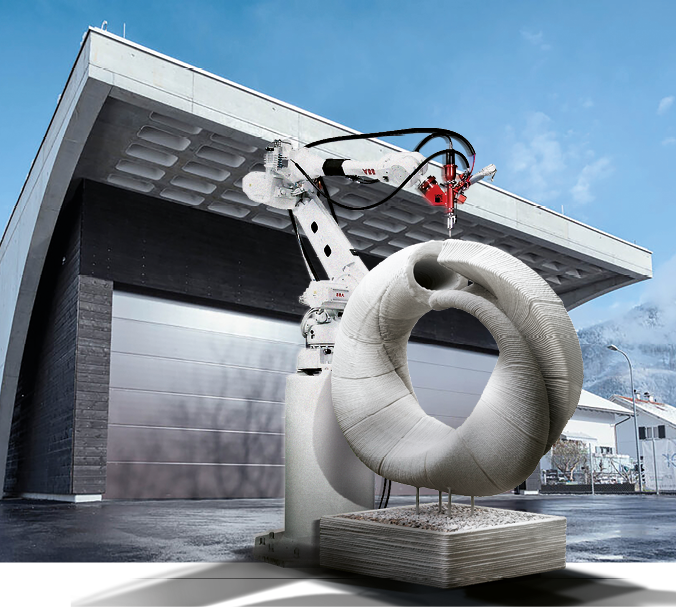
Umieszczasz materiał tam, gdzie go potrzebujesz. Zostawiasz go tam, gdzie go nie potrzebujesz.
Wielki cel na przyszłość? Aby drukować bezpośrednio na placu budowy!
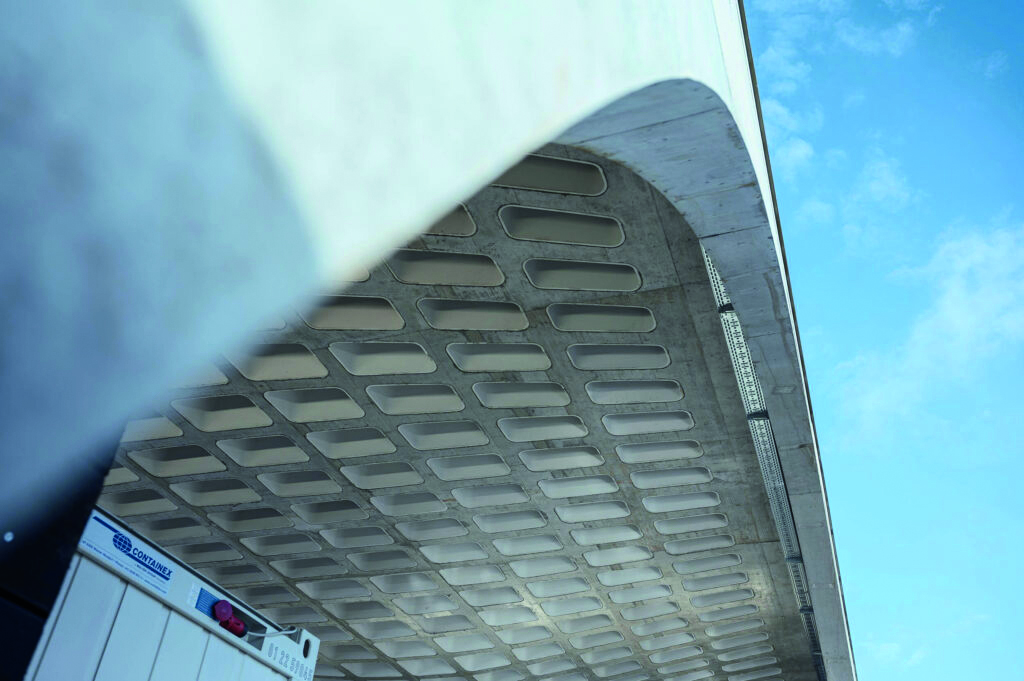