
STAR HOURBauMinator®
Un terzo in meno di cemento e acciaio. 25% in meno di CO2. Per il più grande soffitto al mondo di questo tipo.
Il BauMinator® correva 24 ore su 24,fino a 52 ore alla volta.
Baumit Austria e il suo partner Concrete 3D hanno raggiunto questo obiettivo per la prima volta in Austria. Stanno costruendo un cantiere con componenti intelligenti a peso ridotto utilizzando la stampa di lastre BauMinator®. Come funziona? Con formatori di nicchia stampati in 3D. E la cosa migliore è che soddisfa tutti i criteri per il raggiungimento degli obiettivi climatici del 2030.
Più lungo e più lontano che mai
Il team austriaco Baumit BauMinator®, insieme ai suoi partner di Concrete 3D e dell’Università di Tecnologia di Graz, è riuscito a portare la tecnologia di stampa 3D a un nuovo livello nella stampa dei soffitti. Anche le dimensioni sono enormi. Nuove pietre miliari
sono stati fissati in termini di lunghezza e ampiezza.
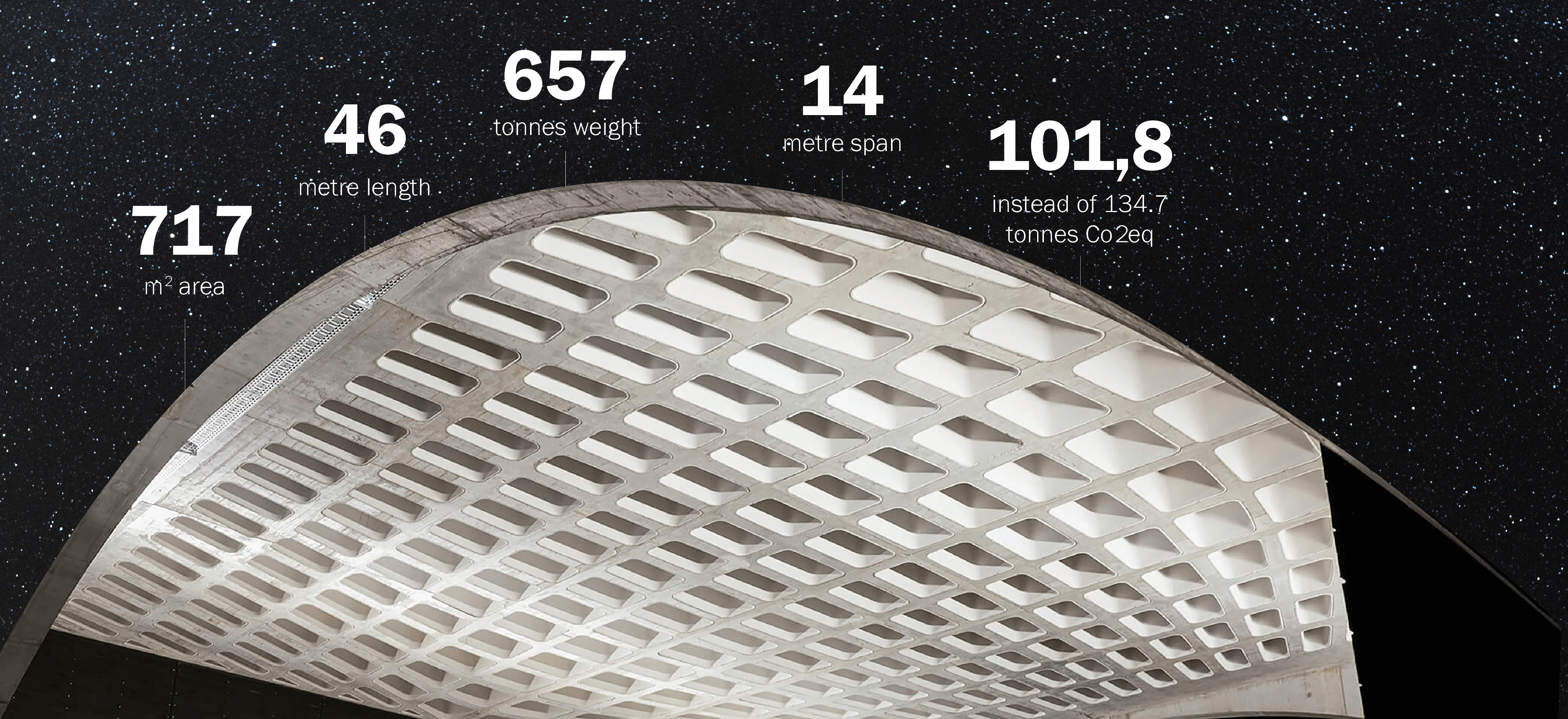
Concentrarsi sul risparmio di materiale
Tutti i partecipanti al progetto hanno cercato di utilizzare il minor materiale possibile. Baumit Austria ha fornito il sistema e il materiale per il progetto. “Con la stampa 3D possiamo utilizzare il calcestruzzo senza alcuna cassaforma. Questa tecnologia ci permette di creare nuove geometrie senza sprechi. In questo modo si risparmiano cemento e acciaio”, spiega Georg Hansemann dell’Università di Tecnologia di Graz.
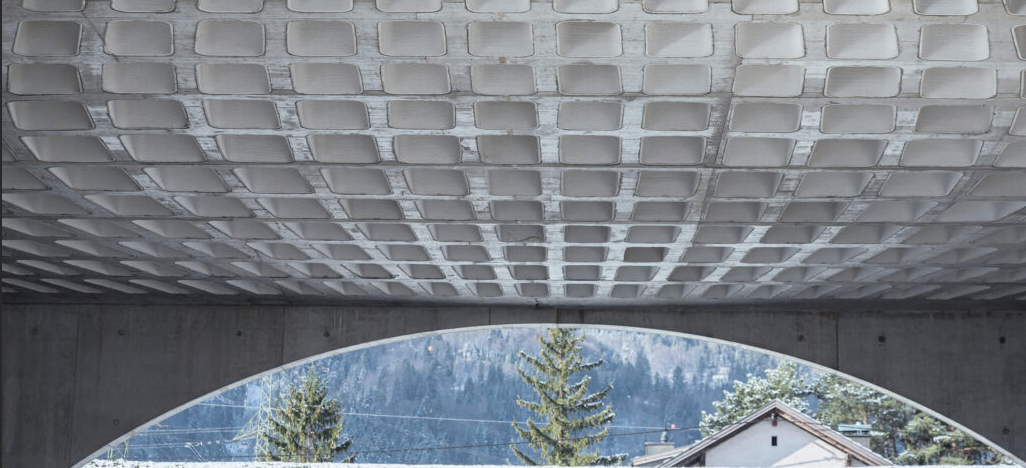
792 corpi di spostamento per il tetto piano, ognuno dei quali è unico, ciascuno numerato.
Soluzione leggera e rispettosa del clima
L’installazione di casseforme perse dalla stampante 3D consente di risparmiare materiale ed emissioni. Utilizzando un software appositamente acquisito, sono stati calcolati 792 corpi di spostamento per il tetto piano di 717 metri quadrati, ognuno unico. Per la stampa sono state utilizzate più di 60 tonnellate di cemento e un totale di 210 chilometri di linea di stampa. Gli elementi, che pesano fino a 80 chilogrammi, sono stati numerati, consegnati in cantiere e posizionati sulla cassaforma con una stazione totale. L’acciaio di rinforzo è stato interposto e il tutto è stato riempito di calcestruzzo. Il risultato è stato un soffitto più leggero di un terzo e la cui produzione ha comportato una riduzione del 24,4% delle emissioni di gas serra.
33 tonnellate di sostanze dannose per il clima gas serra risparmiati durante produzione.
Il più grande soffitto al mondo con questo sistema
L’architetto Marcus Ender illustra le possibilità progettuali di questa tecnologia. “La forma e il posizionamento degli incavi rendono visibile il corso delle forze”. La gestione speciale e la logistica ingegnosa hanno naturalmente comportato costi aggiuntivi. Tuttavia, ciò è stato compensato dal risparmio di materiale e dalle maggiori possibilità strutturali.
Il tetto piano poggia su due archi di sostegno lunghi 46 metri che attraversano due sale in legno.
Un esempio di economia circolare
Il progetto si dimostra anche riciclabile grazie alla composizione dei materiali. La costruzione è interamente costituita da cemento e acciaio e può quindi essere riciclata al 100% al termine della sua vita utile. L’Università di Tecnologia di Graz ha un ulteriore potenziale nell’uso del calcestruzzo a ridotto contenuto di CO2 e nel processo.
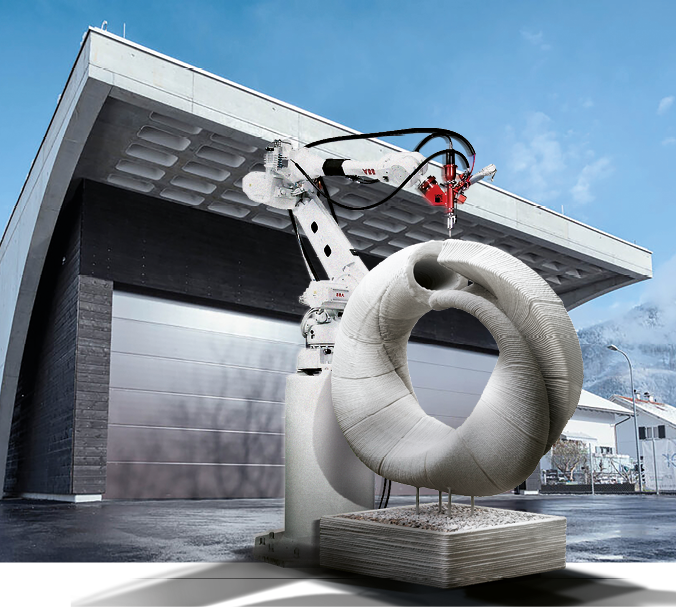
Si posiziona il materiale dove serve. Lo si lascia fuori dove non serve.
Il BauMinator® dà l’esempio di GO2morrow
La sostenibilità in Baumit si chiama GO2morrow. Il soffitto a cassettoni del cantiere di Bludenz è un altro esempio di come la tecnologia di costruzione della stampa 3D guardi al futuro: Il materiale viene posizionato in modo mirato o tagliato direttamente. In questo modo è possibile produrre stampi e progetti che prima erano impossibili o semplicemente troppo costosi. Inoltre, il risparmio del 30-50% del peso dei componenti è un passo significativo verso l’edilizia sostenibile, in quanto si risparmia anche circa un terzo della CO2 associata.
Il grande obiettivo del futuro? Per stampare direttamente in cantiere!
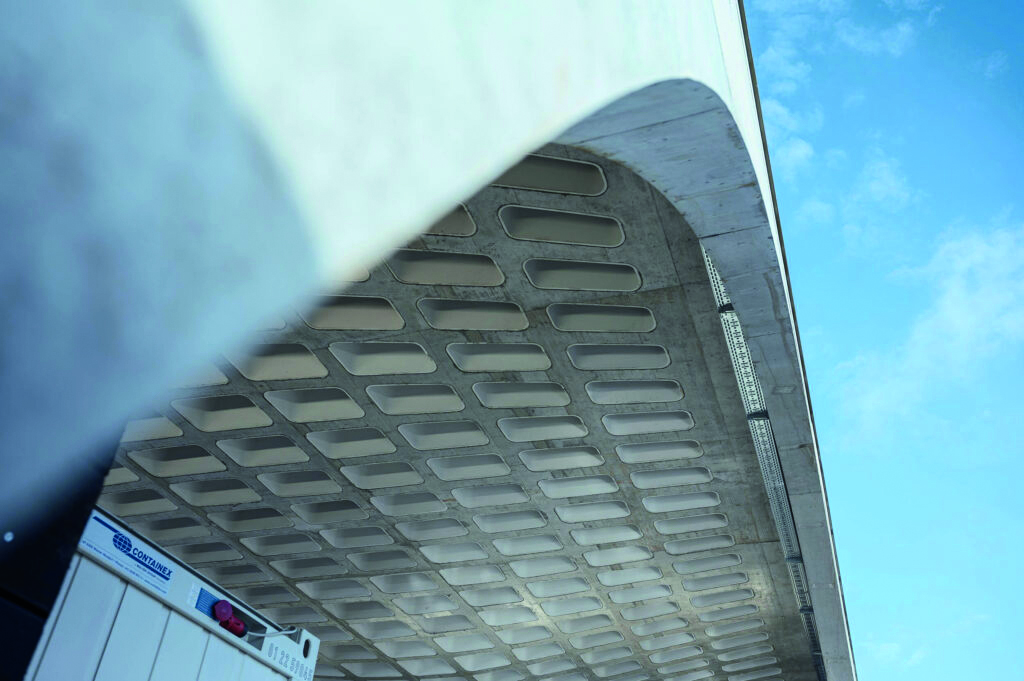