
BauMinator®L'heure des étoiles
Un tiers de béton et d’acier en moins. 25 % de CO2 en moins. Pour le plus grand plafond de ce type au monde.
Le BauMinator® a fonctionné en permanence,jusqu'à 52 heures d'affilée.
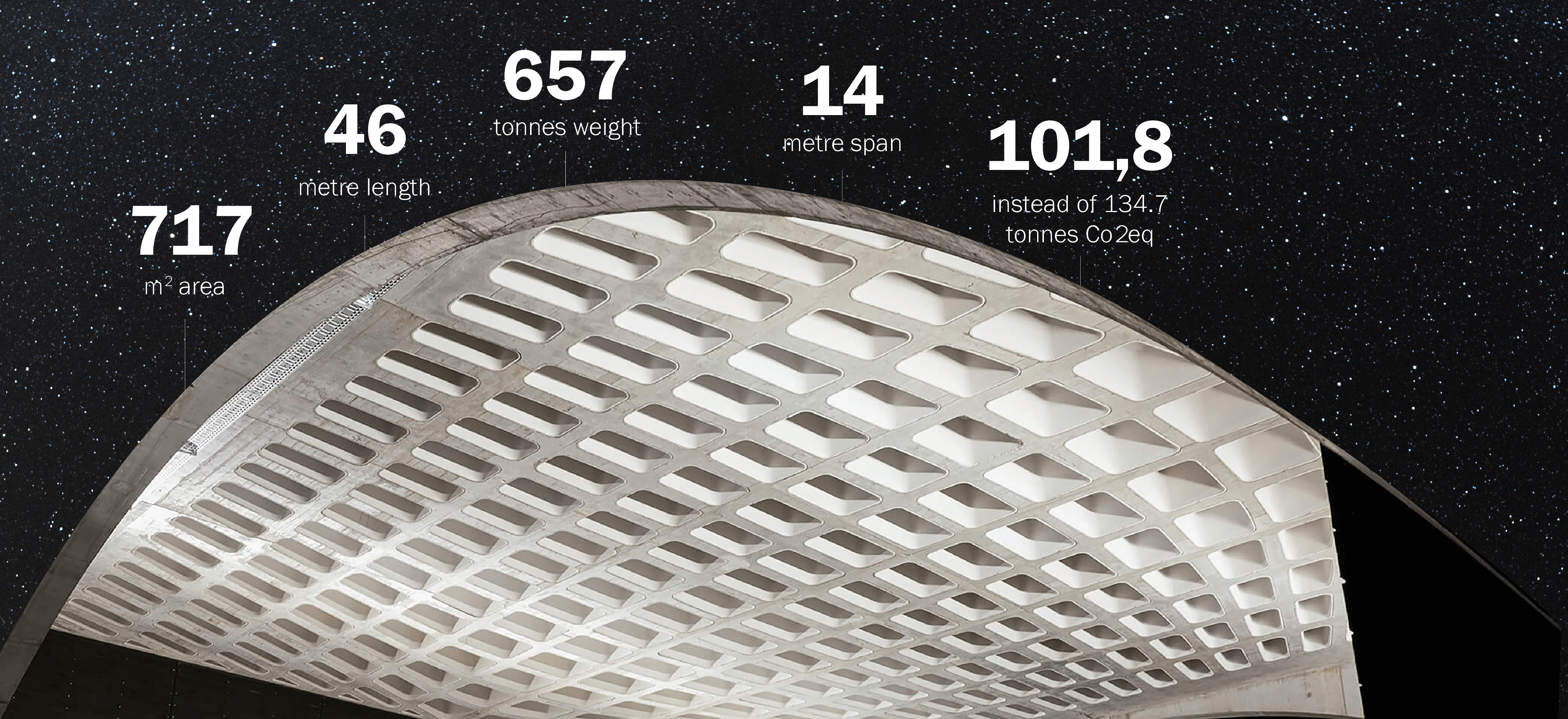
L'accent mis sur l'économie de matériaux
Toutes les personnes impliquées dans le projet se sont efforcées d’utiliser le moins de matériaux possible. Baumit Austria a fourni le système et le matériel pour le projet. « Avec l’impression 3D, nous pouvons utiliser le béton sans aucun coffrage. Cette technologie nous permet de créer de nouvelles géométries sans gaspillage. Cela permet d’économiser du béton et de l’acier », explique Georg Hansemann de l’Université de technologie de Graz.
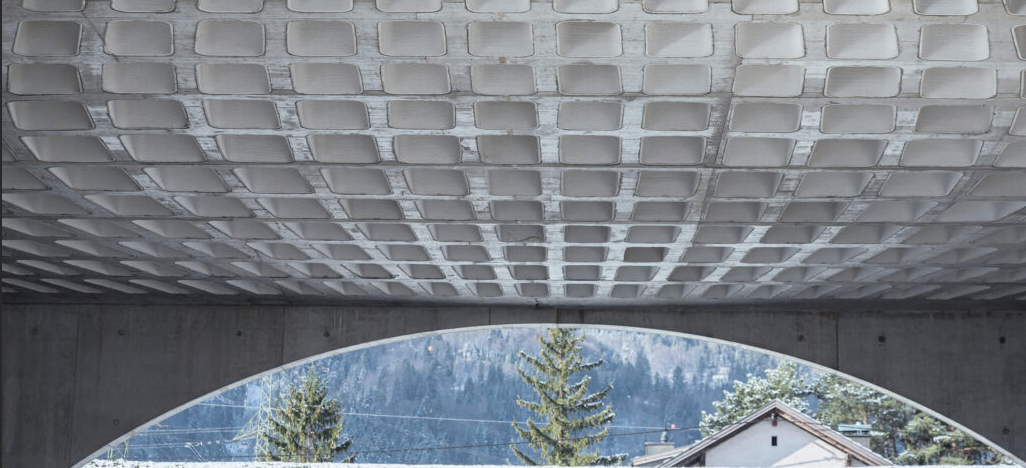
792 corps de déplacement pour le toit plat - chacun d'entre eux est unique, chacun numéroté.
Solution légère et respectueuse du climat
L’installation de coffrages perdus à partir de l’imprimante 3D permet d’économiser des matériaux et de réduire les émissions. À l’aide d’un logiciel spécialement acquis, 792 corps de déplacement ont été calculés pour le toit plat de 717 mètres carrés – chacun d’entre eux étant unique. Ils ont été imprimés en utilisant plus de 60 tonnes de béton et un total de 210 kilomètres de lignes d’impression. Les éléments, pesant jusqu’à 80 kilogrammes, ont été numérotés, livrés sur le chantier et positionnés sur le coffrage à l’aide d’une station totale. De l’acier d’armature a été posé entre les deux et l’ensemble a été rempli de béton. Le résultat satisfaisant a été un plafond un tiers plus léger et dont la production a émis 24,4 % de gaz à effet de serre en moins.
33 tonnes de substances nocives pour le climat de gaz à effet de serre économisés pendant production.
Le plus grand plafond du monde équipé de ce système
L’architecte Marcus Ender souligne les possibilités de conception offertes par cette technologie. « La forme et l’emplacement des évidements rendent visible le cheminement des forces. Le traitement spécial et la logistique ingénieuse ont naturellement entraîné des coûts supplémentaires. Toutefois, les économies de matériaux et les possibilités structurelles accrues ont compensé ce manque.
Le toit plat repose sur deux Des arcs de soutien de 46 mètres de long qui enjambent deux salles en bois.
Un exemple d’économie circulaire
Le projet s’avère également recyclable en raison de la composition des matériaux. La construction est entièrement constituée de béton et d’acier et peut donc être recyclée à 100 % à la fin de sa vie utile. L’Université de technologie de Graz dispose d’un potentiel supplémentaire dans l’utilisation du béton à teneur réduite en CO2 ainsi que dans le processus.
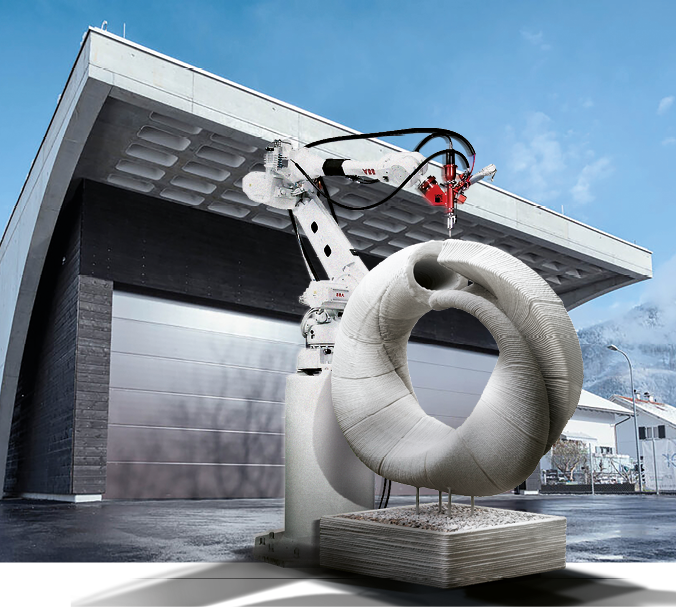
Vous placez le matériel là où vous en avez besoin. Vous le laissez là où vous n'en avez pas besoin.
Le grand objectif de l'avenir ? Pour imprimer directement sur le chantier!
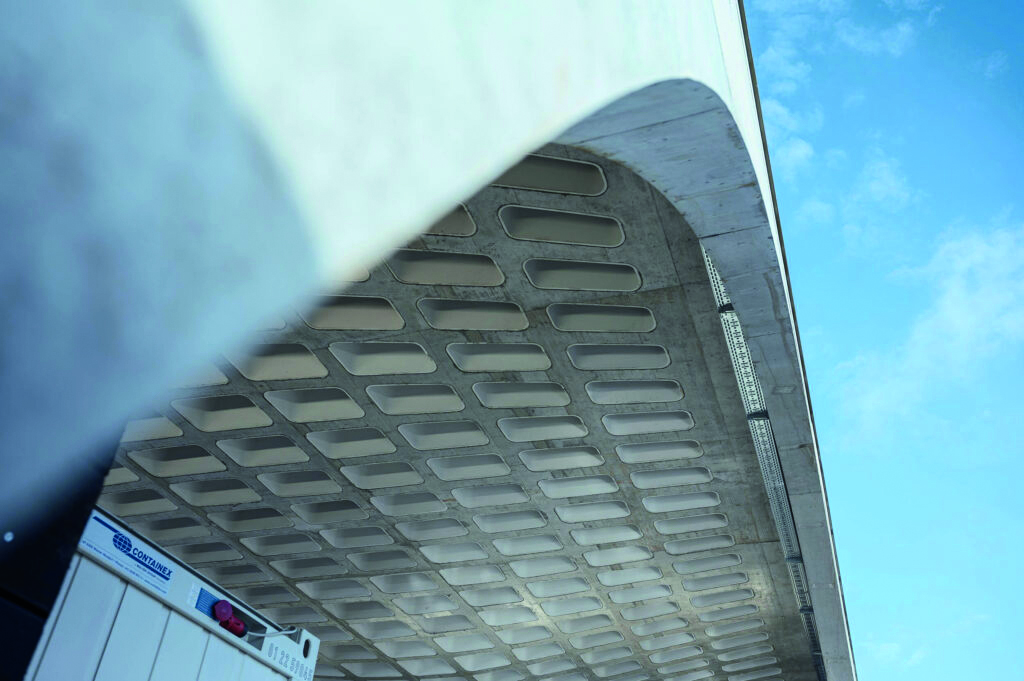