
STAR HOURBauMinator®
One third less concrete and steel. 25% less CO2. For the world’s largest ceiling of its kind.
The BauMinator® ran around the clock,up to 52 hours at a time.
Longer and further than ever before
The Austrian Baumit BauMinator® team, together with its partners from Concrete 3D and Graz University of Technology, has succeeded in taking 3D printing technology to a new level in ceiling printing. The dimensions are also enormous. New milestones
have been set in terms of length and span.
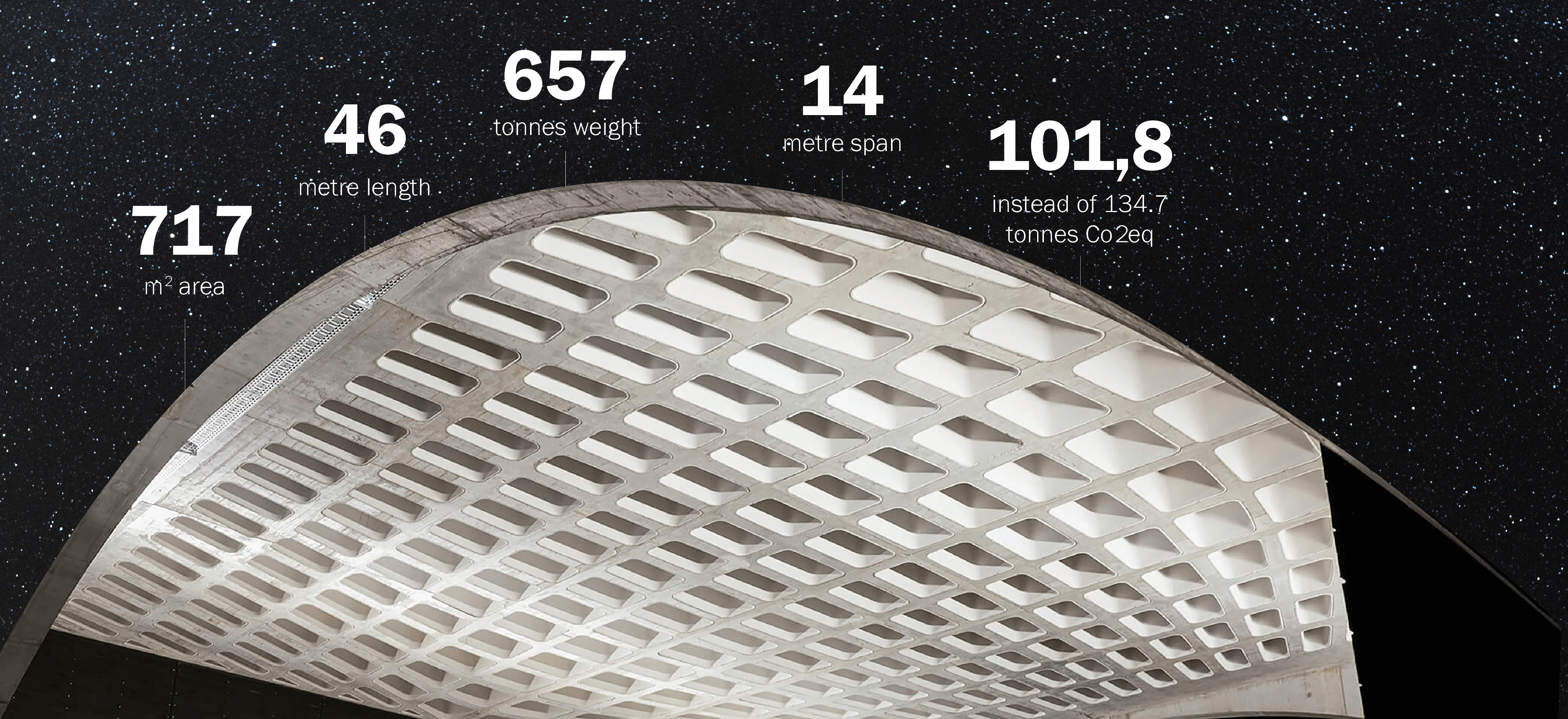
Focus on saving material
Everyone involved in the project aimed to use as little material as possible. Baumit Austria provided the system and material for the project. “With 3D printing, we can use concrete without any formwork. This technology allows us to create new geometries without waste. This saves concrete and steel,” explains Georg Hansemann from Graz University of Technology.
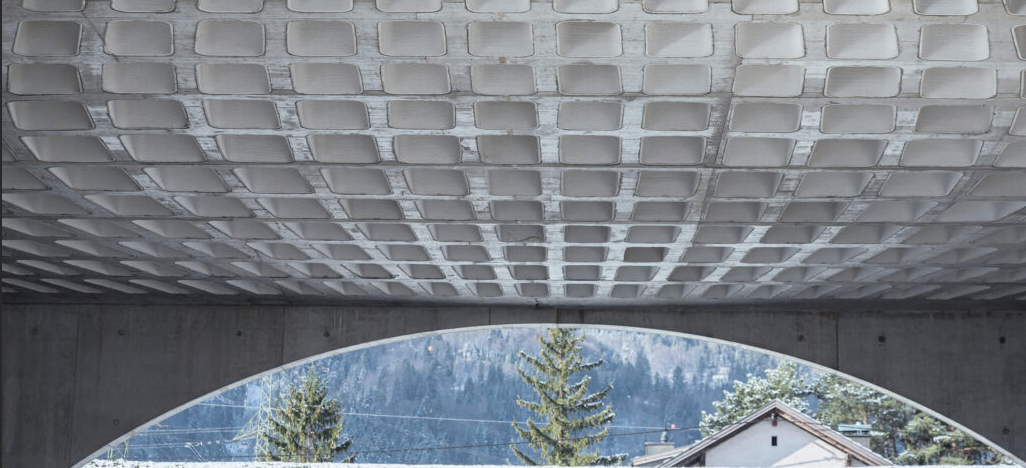
792 displacement bodies for the flat roof – each unique, each numbered.
Lightweight and climate-friendly solution
The installation of lost formwork from the 3D printer saves material and emissions. Using specially acquired software, 792 displacement bodies were calculated for the 717 square metre flat roof – each one unique. These were printed using more than 60 tonnes of concrete and a total of 210 kilometres of printing line. The elements, weighing up to 80 kilograms, were numbered, delivered to the construction site and positioned on the formwork using a total station. Reinforcing steel was laid in between and the whole thing was filled with concrete. The pleasing result was a ceiling that was a third lighter and whose production emitted 24.4% less greenhouse gases.
33 tonnes of climate-damaging greenhouse gas saved during production.
The world’s largest ceiling with this system
Architect Marcus Ender points out the design possibilities of the technology. “The shape and positioning of the recesses make the course of the forces visible.” The special handling and ingenious logistics naturally resulted in additional costs. However, this was compensated for by the material savings and the extended structural possibilities.
The flat roof rests on two 46-metre-long supporting arches that span two wooden halls.
An example of the circular economy
The project also proves to be recyclable due to the material composition. The construction consists entirely of concrete and steel and can therefore be 100% recycled at the end of its useful life. There is further potential for Graz University of Technology in the use of CO2-reduced concrete as well as in the process.
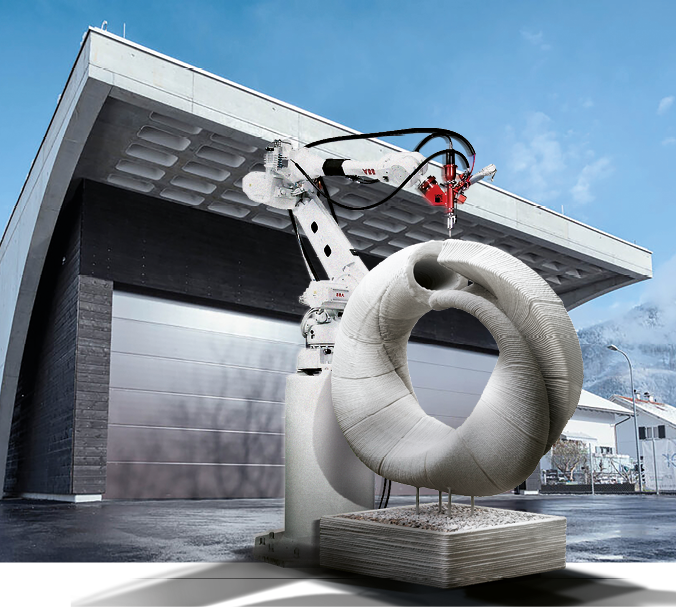
You place material where you need it. You leave it out where you don’t need it.
The BauMinator® sets an example for GO2morrow
Sustainability at Baumit is called GO2morrow. The coffered ceiling of the Bludenz building yard is another example of how 3D printing construction technology is looking to the future: Material is placed in a targeted manner or cut out straight away. In this way, moulds and designs can be produced that were previously either impossible or simply too expensive. Furthermore, saving 30% to 50% of the weight of the components is also a significant step towards sustainable construction, as around a third of the associated CO2 is also saved.
The big goal of the future? To print directly on the construction site!
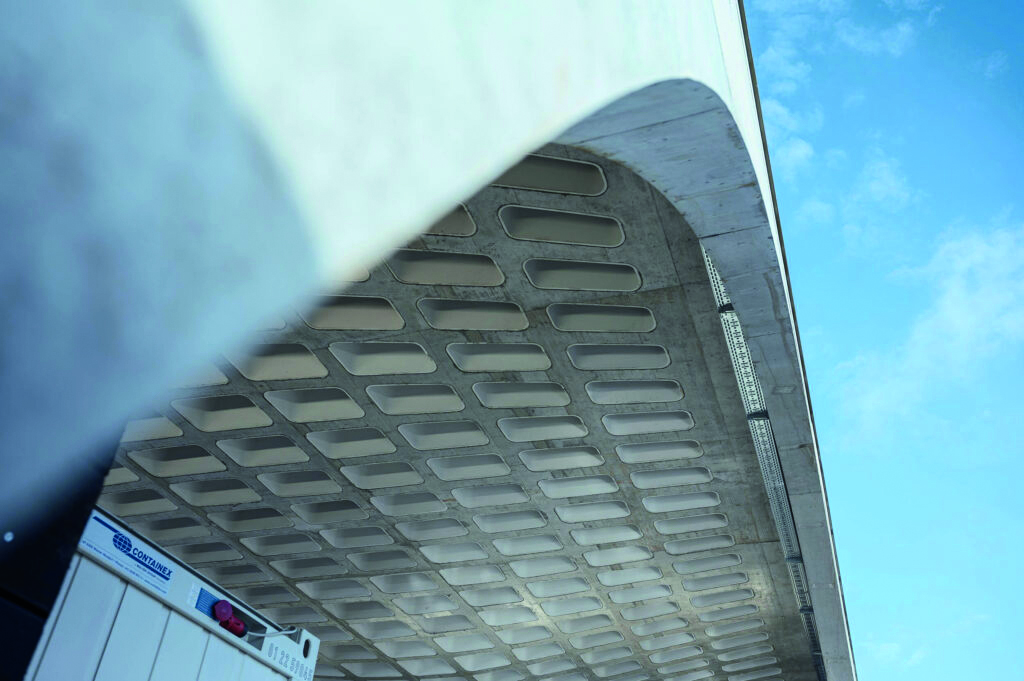