
STERNSTUNDE BAUMINATOR®
Ein Drittel weniger Beton und Stahl. 25 % weniger CO2. Für die weltweit größte Decke dieser Art.
Der BauMinator® lief rund um die Uhr, bis zu 52 Stunden am Stück.
Das gelang Baumit Österreich und seinem Partner Concrete 3D erstmalig in Österreich. Sie bauen mit dem BauMinator® Deckendruck einen Bauhof mit gewichtsreduzierten intelligenten Bauteilen. Wie das funktioniert? Mit 3D-gedruckten Aussparungskörpern. Und das Beste daran: Es werden alle Kriterien zur Erreichung der Klimaziele 2030 erfüllt.
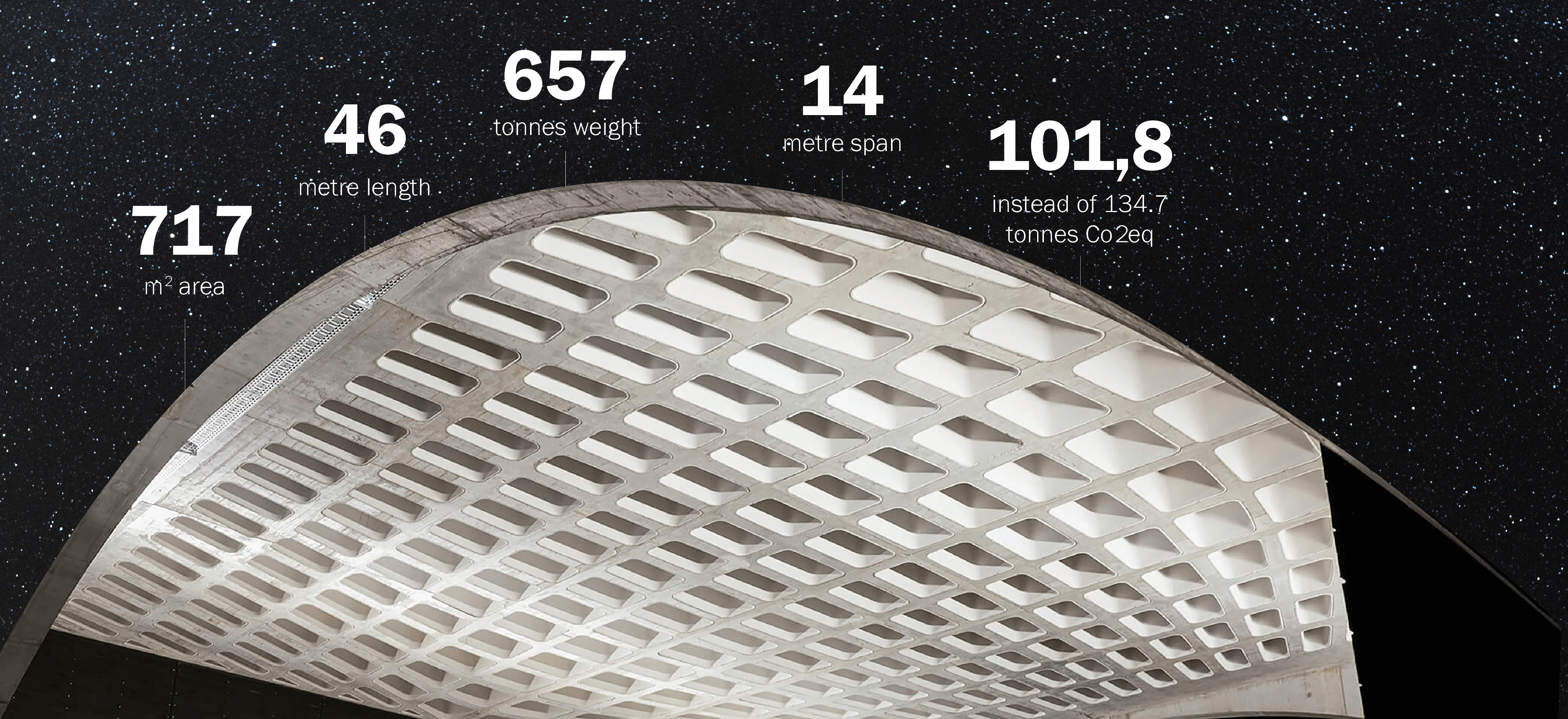
Material sparen im Fokus
Alle am Projekt Beteiligten hatten das Ziel, so wenig Material wie möglich zu verwenden. Baumit Österreich stellte das System und Material für das Projekt bei. „Mit 3D-Druck können wir Beton ganz ohne Schalung einsetzen. Mit dieser Technik lassen sich neue Geometrien abfallfrei erzeugen. So sparen wir Beton und Stahl,“ erklärt Georg Hansemann von der Technischen Universität Graz.
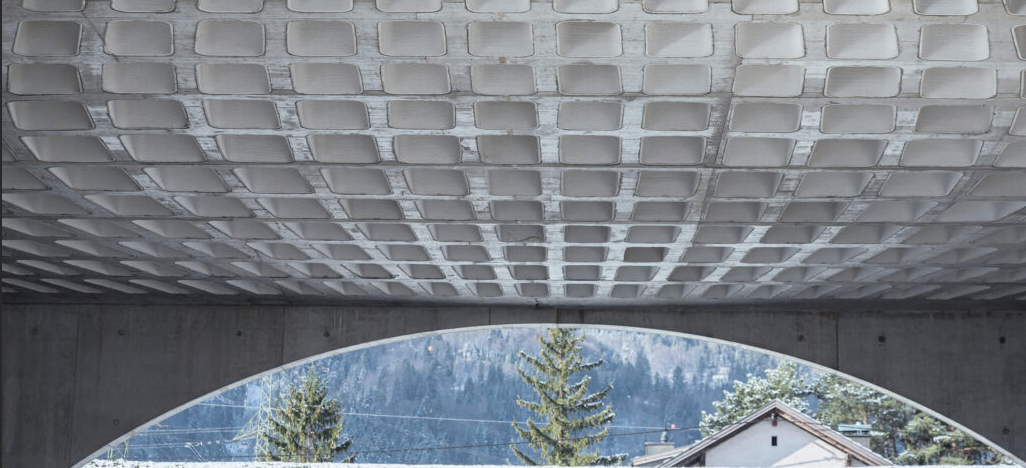
792 Verdrängungskörper für das Flachdach – jeder einzigartig, jeder nummeriert.
Leicht und klimaschonend gelöst
Durch den Einbau verlorener Schalungen aus dem 3D-Drucker werden Material und Emissionen gespart. Mit einer eigens angeschafften Software berechnete man für das 717 Quadratmeter große Flachdach 792 Verdrängungskörper – jeder ein Unikat. Diese wurden mit mehr als 60 Tonnen Beton und einer insgesamt 210 Kilometer langen Druckbahn gedruckt. Die bis zu 80 Kilogramm schweren Elemente wurden nummeriert, auf die Baustelle geliefert und dort mittels Totalstation auf der Schalung positioniert. Dazwischen wurde Bewehrungsstahl verlegt und das Ganze mit Beton aufgefüllt. Das erfreuliche Ergebnis war eine um ein Drittel leichtere Decke, deren Herstellung 24,4 % weniger Treibhausgase emittierte.
33 Tonnen klimaschädliches Treibhausgas bei der Herstellung gespart.
Die weltweit größte Decke mit diesem System
Architekt Marcus Ender weist auf die gestalterischen Möglichkeiten der Technik hin. „Die Form und Positionierung der Aussparungen lassen den Verlauf der Kräfte sichtbar werden.“ Durch das besondere Handling und die ausgeklügelte Logistik entstand natürlich auch ein Mehraufwand. Dieser wurde jedoch durch die Materialeinsparung und die erweiterten
statischen Möglichkeiten wieder kompensiert.
Das Flachdach ruht auf zwei 46 Meter langen Stützbögen, die zwei Holzhallen überspannen.
Ein Beispiel für Kreislaufwirtschaft
Das Projekt erweist sich aufgrund der Materialzusammensetzung außerdem als kreislauffähig. Die Konstruktion besteht ausnahmslos aus Beton und Stahl und kann daher am Ende ihrer Nutzungsdauer zu 100 % recycelt werden. Weiteres Potenzial steckt für die Technische Universität Graz im Einsatz von CO2-reduziertem Beton sowie auch beim Prozess.
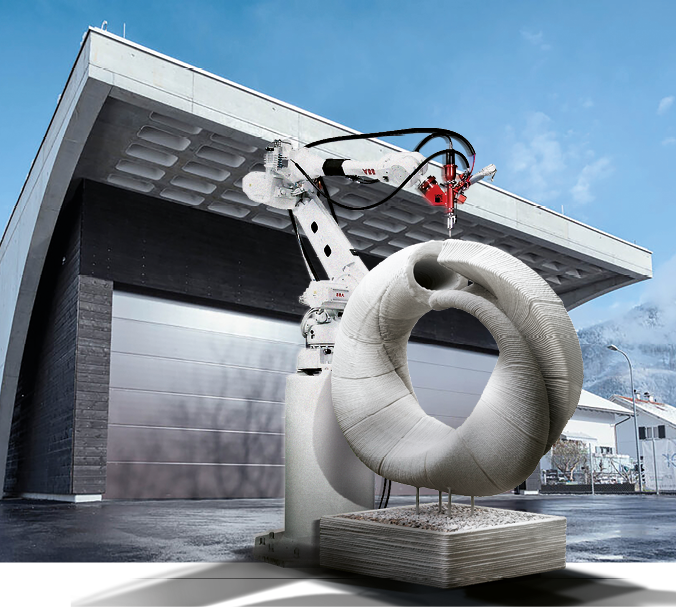
Man platziert Material dort, wo man es braucht. Man lässt es weg, wo man es nicht braucht.
Der BauMinator® setzt ein Zeichen für GO2morrow
Nachhaltigkeit bei Baumit heißt GO2morrow. Die Kassettendecke des Bauhofs Bludenz ist ein weiteres Beispiel dafür, dass die 3D-Druck-Bautechnologie in die Zukunft schaut: Material wird gezielt platziert oder gleich ausgespart. Auf diese Weise kann man Formen und Designs anfertigen, die bisher entweder unmöglich oder einfach zu teuer waren. Weiters ist die Einsparung von 30 % bis 50 % des Gewichts der Bauteile auch ein bedeutender Schritt in Richtung nachhaltiges Bauen, da auch ungefähr ein Drittel des damit verbundenen CO2eingespart wird.
Das große Ziel der Zukunft? Direkt auf der Baustelle zu drucken!
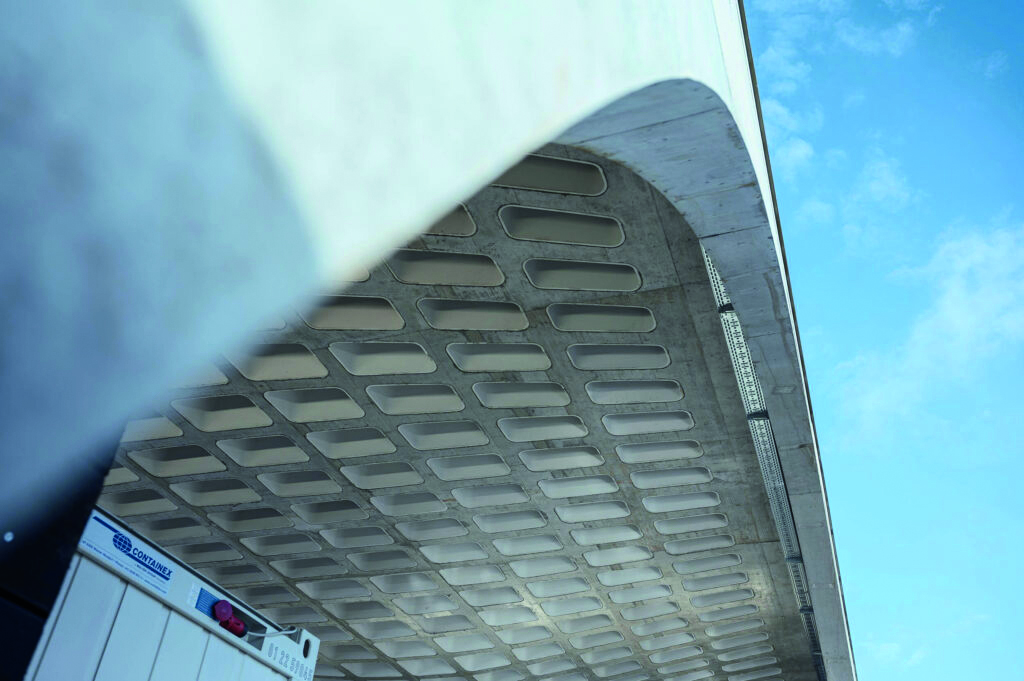